기후변화는 인류가 직면한 가장 심각한 문제입니다. 그 주범으로는 온실가스, 특히 이산화탄소(CO2)가 지목됩니다. 오늘날 대기 중 이산화탄소 농도는 약 415 ppm으로 산업혁명 이전의 280 ppm에 비해 매우 높은 수준입니다. 그런데, 아주 오래 전으로 돌아가보면 백악기(6,600만년~1.45억년 전)에는 2,000 ppm, 캄브리아기(4.4억년~4.8억년 전)에는 5,000 ppm 정도로 지금으로서는 상상할 수 없을 만큼 대기 중 이산화탄소 농도가 높았습니다.
그렇다면 그 많던 대기 중 이산화탄소는 다 어디로 갔을까요?
답은 바로 탄산염암에 있습니다 대기 중의 이산화탄소 농도가 높아지면 해수 중 탄산이온 농도가 증가되고, 석회암을 포함한 탄산염암의 퇴적이 쉽게 발생될 수 있는 분위기가 만들어집니다. 따뜻하고 깨끗한 얕은 바다에서 서식하는 산호, 조개, 각종 조류 등 다양한 생물체들은 보호용 껍질이나 몸체를 만들기 위해 해수에 용존된 칼슘이온(Ca2+)과 탄산이온(CO32-)을 뽑아내어 방해석이나 아라고나이트와 같은 탄산칼슘 물질을 만듭니다. 이 탄산칼슘 물질은 높은 수온으로 인해 이산화탄소(CO2)의 탈기(脫氣)가 쉽게 일어나 탄산칼슘(CaCO3)의 침전이 용이해집니다. 이렇게 만들어진 탄산칼슘 물질이 쌓이고 굳어져 석회암이 만들어집니다. 실제로 대기 중의 이산화탄소 농도가 높았던 캄브리아기와 백악기는 전 세계적으로 석회암이 많이 만들어졌던 시기로 알려져 있습니다.
즉, 탄산염암은 지구상에서 이산화탄소를 가장 많이 보유하고 있는 초대형 이산화탄소 저장고라고 할 수 있습니다.
전 세계적으로 도시화가 진행되면서 콘크리트의 수요는 지속적으로 늘고 있습니다. 집, 도로, 교량, 고층빌딩, 공장까지 콘크리트로 건설되고 있죠. 인류가 1년간 소비하는 콘크리트는 약 41억 톤을 넘는다고 합니다. 물을 제외한 다른 어떤 물질보다 많이 사용되고 있습니다. 지금 이 순간도 대부분의 사람이 콘크리트 위에 서거나 앉아 있을 것입니다.
이것이 문제가 됩니다. 왜냐하면 콘크리트, 특히 그 주원료인 시멘트가 환경에 부정적인 영향을 미치기 때문입니다. 시멘트 산업은 연간 28억 톤의 이산화탄소를 배출합니다. 이 수치는 중국과 미국을 제외한 모든 나라의 연간 이산화탄소 배출량을 웃도는 양으로, 인간이 배출하는 이산화탄소의 4~8%에 해당합니다.
지구의 기온 상승을 1.5℃ 이하로 억제하고 2℃를 결코 초과하지 않는다는 파리협정의 목표를 달성하기 위해서는 시멘트 생산으로 배출되는 CO2의 양을 2030년까지 최소 16% 삭감할 필요가 있습니다. 그러나 현재는 중국에서 여러 가지 진행중인 대규모 건축 프로젝트 등의 이유로 CO2 배출량은 계속 증가하고 있습니다. 콘크리트 업계는 제한된 시간 내에서 문제를 해결해야 하는 어려움을 겪고 있습니다.
발상의 전환 – CO2를 콘크리트에 가두기
콘크리트를 만드는 방법은 19세기 이후 거의 변하지 않았습니다. 자갈, 모래, 시멘트, 그리고 물을 섞는 것이죠. 콘크리트의 최대의 문제점은 시멘트를 만드는 방법에 있습니다. 시멘트를 만들려면 우선 클링커를 만들어야 합니다. 클링커는 석회, 점토, 석고 등 다양한 재료를 섞어 소성로(킬른)에서 만들어집니다.
클링커는 1,500℃ 이상의 고온에서 연소해야 만들어지는데요, 바로 그 과정에서 대량의 CO2가 배출됩니다. 게다가 소성로에서 석회(탄산칼슘)가 산화칼슘(CaO)으로 분해되면서 더 많은 CO2가 방출됩니다. 그래서 시멘트 대용으로 플라이애시, 슬래그 등을 사용하여 콘크리트를 만들기도 합니다.
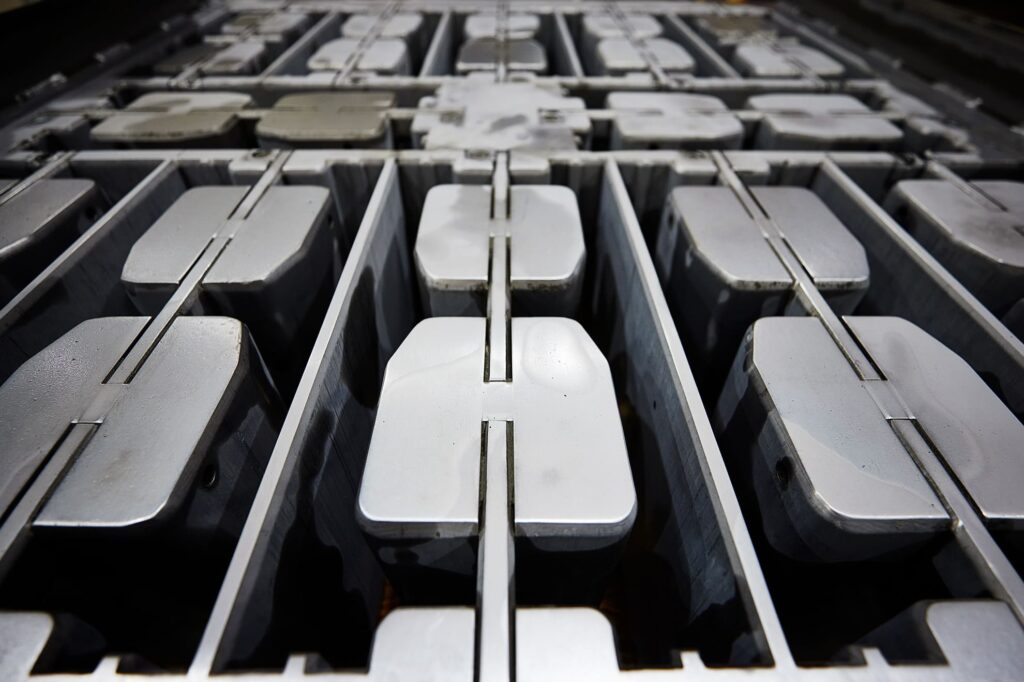
캐나다의 콘크리트 메이커인 카비크리트(Carbicrete)는 시멘트가 없고, 탄소배출이 네거티브인 프리캐스트 콘크리트를 생산합니다. 카비크리트는 시멘트 대신 슬래그를 사용하여 탄소 배출을 줄이고 프리캐스트 콘트리트를 생산할 때 원재료를 혼합한 후 콘크리트를 굳히는 경화 공정에서 이산화탄소를 사용합니다. 산업현장에서 배출되는 CO2를 포집하고 운송하여 콘크리트에 주입하고 화학반응에 의해 탄산칼슘(CaCo3), 즉 석회를 생성시켜 경화하는 것입니다. 생성된 탄산염 콘크리트는 기존 콘크리트보다 압축 강도가 최대 30% 더 높습니다.
카비크리트는 제품 생산 공정에서 이산화탄소 배출량보다 흡수량이 많은 카본 네거티브(Carbon Negative) 기업입니다. 현재 카비크리트의 경화 공정은 신중하게 통제된 환경에서만 수행할 수 있으며 건설 현장에 배송되기 전에 프리케스트 콘크리트 제품으로 사용을 제한되고 액상 레미콘에서는 사용할 수 없습니다.
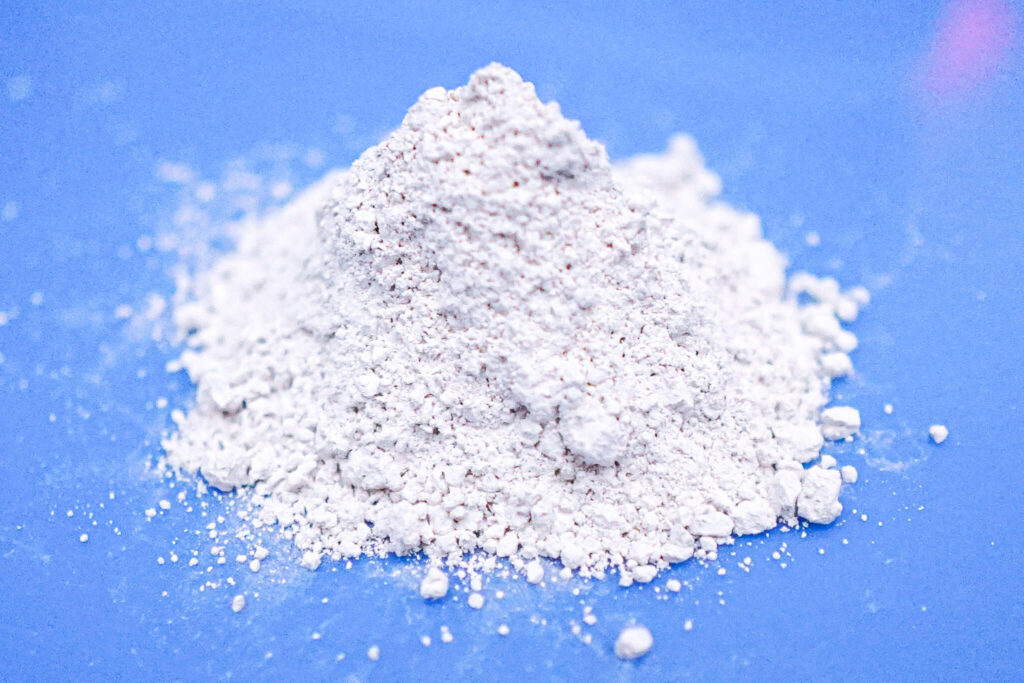
이산화탄소로 경화하는 콘크리트 생산량을 늘리는 기업으로 솔리디아 테크놀로지스(Solidia Technologies)가 유명합니다. 이 회사는 시멘트에 사용되는 석회의 양을 줄이고 천연 및 합성 규회석을 포함한 점토를 늘려 소성 온도를 낮추는 데 성공하여 연료 소비량과 CO2 배출량을 각각 30% 삭감할 수 있다고 합니다. 또 이런 저석회 시멘트를 경화하기 위해 물 대신 이산화탄소를 사용하여 탄소를 최대 70%까지 줄입니다.
경화에 물 대신 CO2를 사용하면 물을 절약할 수 있습니다. 일반적인 포틀랜드 시멘트로 콘크리트를 만들 때 소비되는 물의 양은 연간 약 2.6조 리터가 되는 데, 솔리디아는 경화 공정에 사용되는 물의 양을 90% 이상 줄일 수 있어서 물 부족 문제에 해결책을 제시하기도 합니다.
지역의 상황에 맞는 솔루션이 필요
콘크리트의 문제를 해결하기 위해서는 시야를 넓힐 필요가 있습니다. 중국과 인도, 두 나라의 콘크리트 생산량이 전체의 63%를 차지하고, 남반구의 개발도상국에서의 수요도 계속 증가하고 있습니다. 그런데 콘크리트는 사용되는 지역에서 생산되고 소비되기 때문에 전세계 공통으로 적용할 수 있는 단일 해결책이 존재하지 않을 가능성이 큽니다.
또, 콘크리트의 탈탄소화는 건축의 방식을 바꾸는 일이 될 수도 있습니다. 많은 건축가나 건설회사가 콘크리트를 대체하는 소재 활용을 고려 중입니다. 목재나 금속, 유리 같은 소재를 더 많이 도입하려 합니다. 레고 블록과 비슷한 콘크리트 블록을 제조하는 연구도 활발히 진행 중이죠. 벽돌 형태로 성형된 콘크리트 블록은 시멘트가 아닌 탄소섬유 또는 강화 폴리머로 강도를 유지하고 볼트로 보강되어 사용이 끝난 후에도 재사용 할 수도 있습니다.
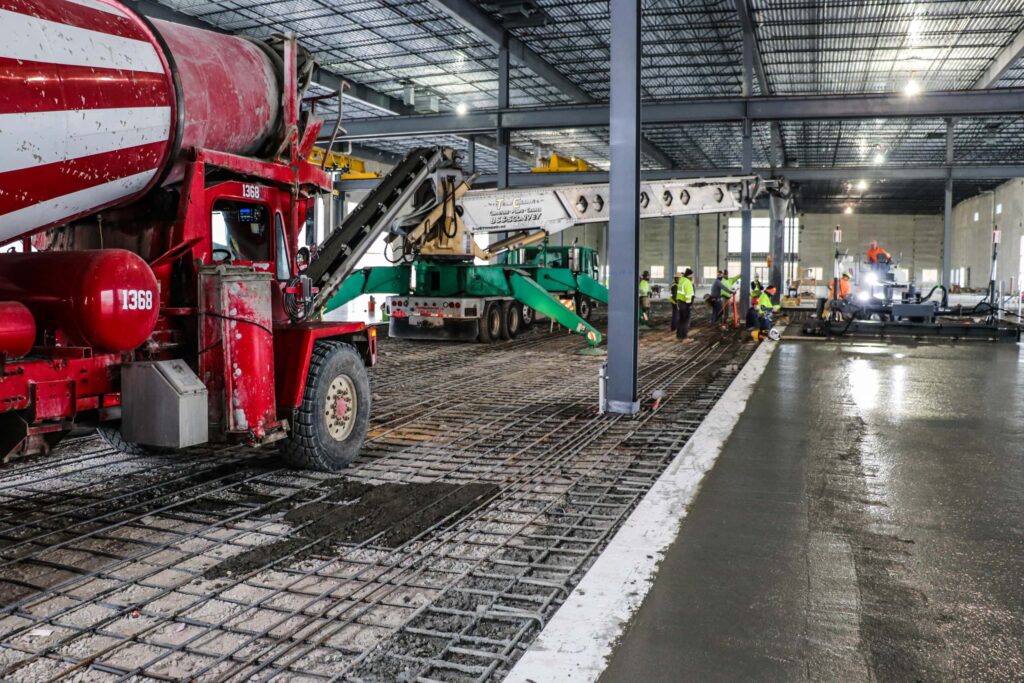
탄소포집이라는 이산화탄소 회수 기술은 발전소 및 철강산업과 같은 대규모 프로젝트에 적합합니다. 대량의 이산화탄소를 단번에 회수할 수 있기 때문입니다. 이렇게 포집한 이산화탄소를 활용하자는 것이 CCU(Carbon Capture Utilization)입니다. 캐나다의 환경기술 기업인 카본큐어(CarbonCure)는 산업 현장에서 배출되는 이산화탄소를 포집하여 액상으로 만들고 레미콘 제조시 주입하여 고정화하는 기술을 제공합니다. 콘크리트의 실질적인 이산화탄소 발생량을 절감할 수 있고 탄소포집격리(Carbon Capture Sequestration)보다 상대적으로 대처하기 쉬운 규모입니다.
카본큐어는 콘크리트 믹서로 혼합할 때 액화 이산화탄소를 분사합니다. 분사된 액화 이산화탄소는 혼합에 사용하는 물에 녹아 탄산 이온이 되고, 시멘트에서 용출한 칼슘 이온과 결합해 수화열 반응이 일어납니다. 탄산염 이온과 시멘트에서 용출된 칼슘 이온은 순간적으로 탄산칼슘은 형성합니다. 탄소광물화가 되는 것이죠. 탄산칼슘은 시멘트의 수화 제품에 증착되어 핵심 강도를 증가시킵니다. 카본큐어는 이 공정을 사용하여 이산화탄소를 가둔 콘크리트를 만듭니다. 콘크리트의 강도를 약 10 % 향상되고, 콘크리트 내에 고정된 이산화탄소는 750 ℃ 이상으로 가열되지 않는 한 다시 방출되지 않습니다. 어찌보면 시멘트를 탄산수로 반죽한다는 아이디어입니다.
이산화탄소 광물화로 시멘트 사용을 과거보다 5~8% 절감할 수 있다는 사실도 중요합니다. 시멘트 공정 중 소성 과정에서 다량의 이산화탄소가 발생하기 때문이죠. 따라서 콘크리트 생산시 시멘트를 사용하지 않기 때문에 나타나는 이산화탄소의 배출 억제 효과도 크다고 말할 수 있습니다. 앞으로 콘크리트 건축물은 CO2를 저장하는 탄소의 무덤이 될지도 모릅니다.